Masters Student of Integrated Product Design, University of Pennsylvania,
former Professional Mechanical Engineer
CAPSTONE PROJECT: MULTI-MODE PORTABLE TURRET BLASTER
For the mechanical engineering capstone project, the course tasked us to form teams of 5 and identify and explore a market need, before designing a prototype for this need.
Our team, Team Wildcard, identified the need for a decent recreational foam blaster (eponymously known as “Nerf blasters”) that is meant to be used in a stationary manner. Competitor products identified in this niche were the Nerf Rhinofire and the Nerf Vulcan. The key deficiencies identified in these products were reliability issues and lack of uniqueness over conventional “mobile” blasters. Our solution was a “suitcase blaster”: a repeating blaster that can unfold from a compact container, and has multiple operating modes. By posting a survey on r/Nerf, we determined a group of other features that would be most desirable for our target user.
The selected features were:
-
Easy to carry
-
Quick to deploy
-
Reliable firing (no jamming)
-
High ammo capacity
-
Manual control mode using handles
-
Bluetooth control mode using smartphone


For our prototypes, we decided to use an off-the-shelf foam blaster, the Air Warriors Quantum, as opposed to designing a blaster from scratch, in order to demonstrate our prototype in action. This allowed us to focus our time and effort on aspects of the project that are most innovative. To control the blaster and switch between control modes, we used an Arduino Mega. To rotate the blaster, we decided to use a strong 20 kg-cm servo. Power was to be supplied by a Nerf Rival Rechargeable battery pack, but it was found that power also needed to be drawn from the pack of 6 D-batteries that came with the Quantum. We determined that in order to control the DC motors within the Quantum blaster, we would also need motor relays.
Our final iteration consists of a turret containing the blaster mounted on a base containing the Arduino, the two battery packs, the servo, and relays. Symmetrical carrying handles are attached to the base, and can be flipped down for deployment.
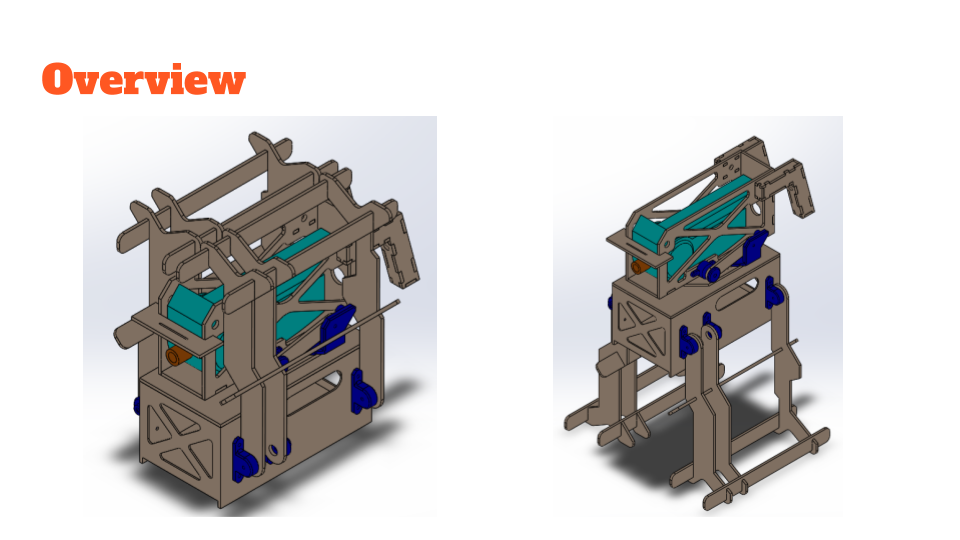
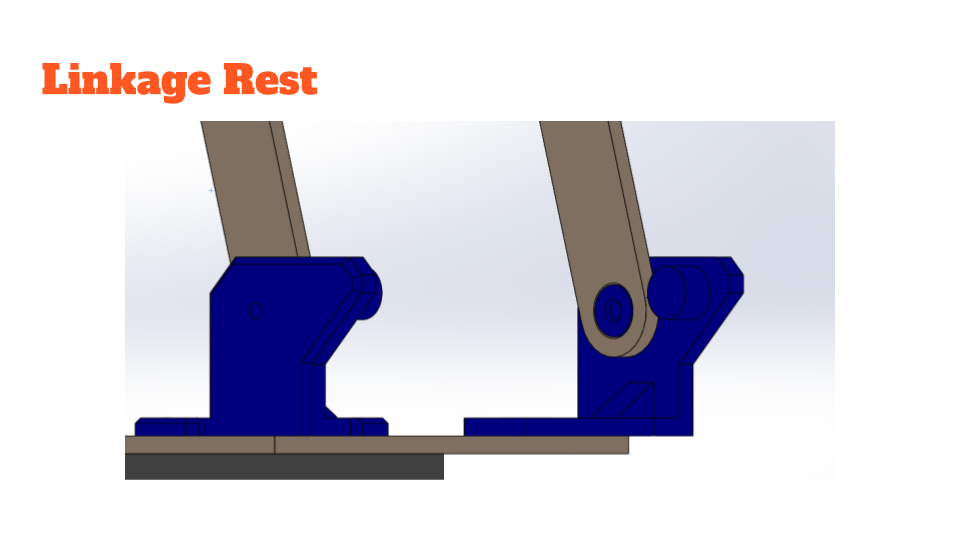

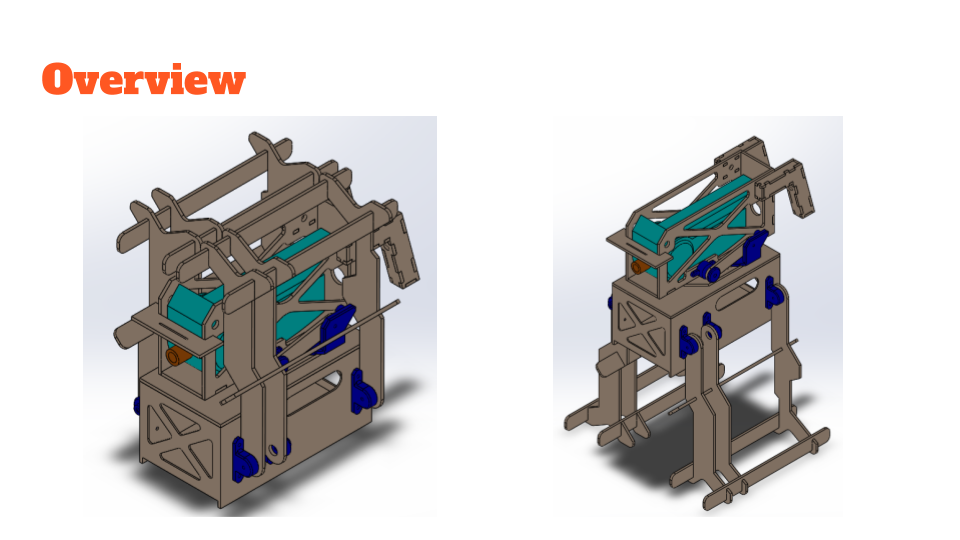